1 高压电动机变频调速的节能意义
中国各种电动机的总耗电量约占全国总消费电量的60%以上,其中,高压电动机与低压电动机对比,数量(台数)比例约为20%∶80%,容量(功率)比例约为60%∶40%。全国宏观年节电能力可达:
25 000 亿kW·h×60%×60%×30%×30%=810亿kW·h。
相当于新建100万kW 机组、年均运行5 000 h的大型发电厂16 座,接近于中国三峡水电站年总发电量。
围绕着高压电动机变频调速也形成了两条技术路线。一条是以高压变频为代表的基于低效率的高压电动机的变频单元串联风险模式的高成本技术路线;另一条是以增容型高- 低压变频方案与Vacon变频器完美结合为代表的基于高压电动机增容提效和变频单元并联冗余模式的低成本技术路线。
2 增容型高- 低压变频方案与Vacon 变频器相结合
增容型高-低压变频调速集成装置,由多功能变压器T、Vacon 变频器LF、利用普通高压电动机通过变换其定子绕组接线结构及线圈绝缘结构改制而成的增容型低压变频调速电动机HM′,以及低压变频/工频切换开关Ct、Cf、Cw所集成,其特征在于增容型低压变频调速电动机HM′采用高压电动机铁心结构;定子绕组采用中压绝缘结构;定子绕组采用低压接线结构;非负荷端轴承采用绝缘结构;低压大容量Vacon 变频器LF 采用输入电压补偿增容措施,如图1所示。
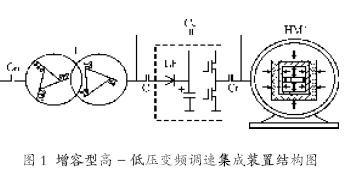
适用范围:
电网电压3~10 kV;
电动机功率200~5 000 kW;
变频器Vacon NX5、NX6系列200~5 000 kW;
变频系统(高压侧)功率因数≥0.95;
变频系统(高压侧)电压总谐波≤1.6%(中国标准GB/T 14549-93《电能质量公共电网谐波》限定值为4%);
运行模式变频/工频,手控/自控,现场/远控,一拖多台;
控制系统PLC,DCS,FCS等。
增容型高- 低压变频方案与Vacon变频器主要结合点如下。
2.1 电动机增容与Vacon变频器工况相结合
众所周知,普通交流电动机的额定功率都是按照正弦波电源设计制造的。变频器提供给电动机的是由高载频脉冲包络而成的准正弦波电源,由于du/dt和di/dt的原因,导致电动机在变频工况下损耗增加,效率和性能比率降低,运行温度升高,额定功率下降。具体表现为:
1)使用变频器导致电机效率降低大约0.5%;
2)附加损耗导致电机升温,在满载下,电机温度更高,对于200 kW 的电机,定子损耗增加10%,热量大约增加18 kW,转子损耗增加100%,转子导电条热量增加大约60 kW;
3)通常降低电机负载以承受更大的损耗。
为此,适度增加电动机额定功率适应变频工况势在必行。采用本增容型高-低压变频方案,即可使普通高压电动机增加额定功率1~3个标准等级,不仅完全弥补了变频工况的功率损失,而且足以达到增产、节能和节材等多重目的。
本方案利用普通高压电动机的机座和铁心结构,改用“中压绝缘结构”和“低压接线结构”,实现低压增容变频调速。中压的范围为1 500~3 000 V,对比6 000 V和10 000 V的“高压绝缘结构”,绝缘厚度可适度减薄1/2~2/3,既能长期承受数倍于额定电压的高载频脉冲产生的自感电势和高次谐波峰值电压的变频工况,又提高了槽满率(导线的占空比>1/3~1/2),使额定功率提高1~3个标准功率等级,效率提高0.5%~3%,功率因数提高0.1~0.2,同功率的高压电动机制造材料消耗可降低10%~20%。
2.1.1 确定高-低压电压等级
本增容型高-低压变频调速集成装置的高压输入电压,即用户的电网电压;而低压则是优选的。优选的原则是,对于560 kW及以下的高压电动机,选择Vacon NX5系列变频器440 V或500 V电压制式;
对于630 kW及以上的高压电动机,为了减少低压电缆压降和线损,宜选择Vacon NX6系列变频器690 V电压制式。
2.1.2 计算定子线圈新匝数
在保持原高压电动机(气隙、定子齿部和轭部)磁通密度不变的前提下,本方案定子线圈匝数W′为
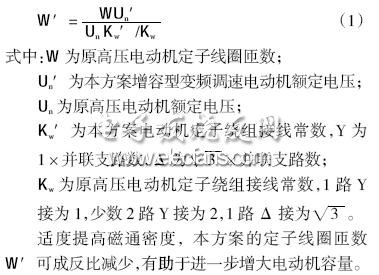
2.2 变压器升压与Vacon变频器增容相结合
Vacon NX5系列变频器的标准电压制式为400~500 V,在中国只能运行在380 V低压动力电源上,可谓大材小用。如若增加一级动力变压器将380 V升至500 V,相当于增加一级变电站,投资大且占地面积亦大,颇不现实。因而导致大量的Vacon变频器欠压运行,造成宝贵资源的无谓浪费。
本方案提供“变频器输入电压补偿”,使Vacon变频器输入电压提升到其额定值的最高限,如440 V或500 V,实现变频器增容10%~30%。即通过一台多功能变压器T,对高压电动机改压后实施降压增容,又对变频器适度升压增容,一举多得。变频器升压增容前的实际输出功率Pp和增容后的最大输出功率P忆max,取决于变频器的最低额定功率Pnmin和最高额定功率Pnmax、最低额定电压Unmin 和最高额定电压Unmax、实际电源电压Up和最大容许工作电压U忆max。
2.3 变压器与Vacon变频器内置电抗器相结合本方案中的多功能变压器T的结构特点在于,一方面,高压绕组与低压绕组实施绝缘隔离,用以隔离来自高压电网的干扰源和来自变频器的高次谐波;另一方面,变压器T的短路阻抗超过4.5%~6%,这与Vacon变频器内置的电抗器结合增加了输入电源的内阻抗,有效缓冲了滤波电容器充电形成的陡峭脉冲波,达到抑制5次、7 次、11次、13次、17次、19次、乃至23次和25次谐波电流并改善变频器功率因数的目的。从而确保高压电网的功率因数≥0.95,电压总谐波≤1.6%,远低于中国标准GB/T14549-93《电能质量公共电网谐波》的限定值4%。
2.4 变压器不接地方式与Vacon变频器T 级EMC相结合
本方案中多功能变压器T的高压侧和低压侧都不接地,对变频器而言,属于“浮动电源”,即“IT 电源”。旨在隔离变频器因输出dv/dt,通过电缆或电机对地的杂散电容产生的共模电流(亦称噪声电流),但在此种状况下要求变频器具有防范高压电网对地电压瞬变的能力。Vacon变频器恰好具有此等级电磁兼容功能,即T级EMC。它采用高阻抗接地方式,即“IT接地方式”,对地仅有一个微小的电流,一方面可有效抑制共模电流,另一方面当变压器高压侧对地发生电压瞬变时,仍能确保变频器的安全运行。
2.5 多相变压器与Vacon多脉冲变频器相结合
依据谐波公式

例如,鞍钢齐大山铁矿第三期变频调速工程,就采用了两台3 相高压输入/6 相1 250 kV·A 低压输出的干式变压器,匹配两台Vacon NX6 系列12 脉冲1 000 kW变频器。2.6 电动机轴承绝缘结构与Vacon变频器良好接地相结合
Vacon培训中心编写的《变频器尺寸测量和变频器计算》中指出造成轴承电流的原因有:
1)磁失衡;
2)电机供电不平衡(电缆、FC);
3)接地电流;
4)轴承损坏及噪音。
通过电子显微镜下的图像,可以看到初期损坏由熔断口导致,末期损坏是凹槽模式。
解决方案是确保电流通道与轴承隔开,措施有:
1)绝缘轴承;
2)接地电刷;
3)变频器、电机和负载之间接地良好;
4)磁环。
本方案电动机非负荷端轴承采用了绝缘结构,即在电机后端盖轴承的外围和两侧加装薄层绝缘材料,然后机械加固。借以切断感生的轴电压和轴电流,从而延长轴承的大修期和使用寿命。
3 综合效益分析
增容型高-低压变频方案与Vacon变频器的完美结合,同国内外高压变频方案对比,具有四“高”、四“低”、四“省”特点。
1)高功率在保持原高压电动机磁通密度和电流密度基本不变、且机械特性容许的条件下,可提高额定功率1~3个标准功率等级。在保持普通低压变频器额定电流不变前提下,可提高其输出功率10%~30%,同时,还可提高传动设备的生产能力10%~20%。
2)高效率本变频系统效率>96%。其中变频器效率为98%,变压器效率为98.8%,电动机的额定效率可提高0.5~5个百分点。
3)高功率因数本变频系统高压侧功率因数可达0.95以上。
4)高可靠性一是采用无油枕全密封变压器或者干式变压器均系免维护类型;二是选用技术成熟的低压大容量变频器安全可靠,使用寿命长达70 000 h;三是利用高等级绝缘的电动机运行在低压变频工况下,绝缘寿命可谓无限长;四是非负荷端轴承采用绝缘结构,切断轴电流和轴电压,从而延长轴承使用寿命;五是备有变频/工频切换开关,一旦变频器发生故障即可及时切换到工频启动—运行模式,即使是工频运行,电动机仍可增容。
5)低谐波本变频系统高压侧电压总谐波<1.6%(国家标准限定值4%)。这是因为本变压器高/低压两侧绕组采取分立式绝缘隔离结构,高压侧或者低压侧采用带有升压线圈的延边三角形连接结构,无零线供电模式,可有效地隔离、吸收和抑制变频过程中产生的高次谐波,使高次谐波分量远低于国家标准限定值。
6)低成本所用全密封无油枕变压器、通用型低压大容量变频器以及变频/工频低压切换开关价格都比常规高压变频装置低得多。比国外高压变频装置单价低50%左右,比国内高压变频装置单价低30%左右。
7)低温升本装置一是实现了变压器、变频器与电动机的电压制式的最佳匹配;二是将电动机绝缘材料合理减薄,使机内冷却空气量增加17%左右,从而有效地降低了电动机运行温升;三是增容而未增载时,即相当于降低电流密度运行,将进一步降低电动机的运行温升,延长其使用寿命。
8)低压安全由于变压器将高/低压隔离,从变压器的输出侧→变频器→电动机的运行电压只有几百伏,颇有安全感,便于操作和维护。
9)省工期本变压器的制造周期只要15~20天;变频器的供货周期只需1~2 月;电动机改压大约1周左右,增容改压大约1 个月左右;控制柜加工不超过1周;安装(包括敷设低压动力电缆和控制屏蔽电缆,无须重打地基和更换对轮)约1 周左右,当天调试当天投运。总施工期(即见效期)仅为0.5~3个月。
10)省投资不但现场改造(电动机改绕定子绕组)成本低,而且新建项目(电动机采用新数据绕制,可节省改制费用和时间)成本更低,即投资省,见效快,投资回收期一般约为1~2年左右。
11)省能源实施本技术方案的微观(单台)节电率为20%~50%,宏观(全国)年节电能力可达600多亿kW·h。
12)省原材料在同等原材料和元器件配置前提下,本方案能提高电动机的额定功率1~3个等级,提高变频器的额定容量5%~25%,即0.5~2个功率等级;在同等功率前提下,本方案可节省制造高压电动机的钢材和矽钢片10%~15%,节约高压绝缘材料40%~60%。